전기차, 에너지 저장 시스템(ESS), 스마트 디바이스 등 다양한 산업에서 배터리는 핵심적인 에너지원으로 자리 잡았습니다. 이처럼 배터리의 중요성이 커지면서, 제조 공정의 품질 관리와 신뢰도 보증은 더욱 중요한 과제가 되고 있습니다. 특히, 배터리 패키징 공정(집전체 연결, 각형 캔 패키징, 버스바 연결)에서 레이저 용접은 배터리 성능과 안전성을 좌우하는 핵심 기술로 꼽힙니다.
레이저 용접은 고정밀 접합, 열 손상 최소화, 생산 효율성 등의 장점으로 배터리 제조 공정에서 필수적인 역할을 합니다. 하지만, 용접 과정에서 발생할 수 있는 미세한 결함(불완전 융합, 균열, 기공 등)은 배터리 성능 저하 및 안전 문제를 초래할 수 있습니다. 이를 해결하기 위해 실시간 모니터링 기술이 필수적으로 도입되고 있으며, 이러한 기술은 공정 안정성 향상과 제품 신뢰도 확보에 중추적인 역할을 합니다.
본 글에서는 배터리 제조 공정에서 레이저 용접의 역할과 중요성을 다루며, 용접 품질을 보증하기 위한 모니터링 및 검사 기술의 원리와 종류를 자세히 살펴보겠습니다. 또한, 각 기술의 장단점을 비교하여 배터리 제조 품질 관리의 핵심 요소를 체계적으로 이해할 수 있는 가이드를 제공합니다.
1️⃣ 배터리 제조에서 레이저 용접의 역할
레이저 용접은 배터리 제조 공정에서 필수적인 접합 기술로, 배터리 셀의 안정성과 성능에 중요한 영향을 미칩니다. 특히, 전기적 연결과 기계적 구조물의 안정성을 확보하기 위해 반드시 사용됩니다.
배터리 제조에서 레이저 용접의 주요 역할
- 전기적 접합 보장
- 전극, 탭, 커넥터와 같은 부품 간의 고품질 접합을 통해 전기 전도성을 최적화합니다.
- 용접 품질이 낮으면 전기 저항이 증가하여 셀 성능에 직접적인 악영향을 미칩니다.
- 기계적 안정성
- 배터리 모듈 및 팩 내부의 구조적 안정성을 보장하여 외부 충격 및 진동에도 견딜 수 있도록 합니다.
- 열 손상 최소화
- 레이저 용접은 열 영향을 받는 영역(HAZ, Heat Affected Zone)을 최소화하여 배터리 셀의 민감한 내부 구조를 보호합니다.
- 생산 효율성 향상
- 고속 용접이 가능하여 대량 생산 환경에 적합합니다.
- 경량화 및 소형화 지원
- 얇은 소재와 복잡한 구조에서도 정밀 용접이 가능하여 제품 설계의 자유도가 높아집니다.
2️⃣ 레이저 용접 품질 관리의 필요성: 모니터링 및 Inspection
레이저 용접 품질 관리가 중요한 이유
배터리 성능과 안전성은 용접 품질에 크게 의존합니다. 불완전 용접, 균열, 기공, 스패터 등 결함은 배터리 전기적 성능 저하, 내부 단락(short circuit), 열 폭주(thermal runaway) 등 심각한 문제를 초래할 수 있습니다. 이를 해결하기 위해 실시간 모니터링을 통해 문제를 조기에 발견하고 생산 공정을 안정화해야 합니다.
모니터링 및 검사 기술의 주요 목적
- 실시간 데이터 수집 및 분석
- 용접 공정 중 이상 징후를 감지하여 불량률을 최소화합니다.
- 결함 예방 및 즉각적인 대응
- 용접 결함을 조기에 탐지해 재작업이나 공정 중단을 줄입니다.
- 최종 제품 신뢰도 확보
- 사후 검사를 통해 배터리의 장기적인 안전성과 품질을 보장합니다.
3️⃣ 레이저 용접 모니터링 기술의 종류
(1) 음향 신호를 이용한 모니터링
음향 신호 모니터링은 레이저 용접 중 발생하는 소리와 음파를 계측하여 용접 상태를 평가하는 기술입니다.
작동 원리
- 용접 중 발생하는 소리(sound)와 음향 방사(acoustic emission)를 마이크로폰 또는 음향 방사 트랜스듀서(AE Transducer)로 감지.
- 특정 주파수 대역에서 발생하는 신호 변화를 분석하여 용접부 결함(균열, 기공, 용입 부족 등)을 평가.
- 주로 용접 재료, 보호가스 노즐, 반사경 등에서 신호를 계측.
특징 및 적용 사례
- 비접촉 방식: 마이크로폰을 통해 비접촉식으로 음향 신호 계측 가능.
- 접촉 방식: AE 트랜스듀서를 용접 재료에 직접 부착하여 높은 신뢰도의 데이터 수집 가능.
장점
- 비용 효율성: 마이크로폰 및 음향 센서를 활용하여 경제적으로 구현 가능.
단점
- 소음 민감성: 주변 소음이나 외란 요소에 의한 신호 왜곡 가능.
- 접촉식 센서의 제한: 재료와의 접촉 필요로 인해 적용 범위가 제한될 수 있음.

(2) 광 신호를 이용한 모니터링
레이저 용접 중 발생하는 플라즈마와 용융 금속에서 방출되는 빛 신호를 분석하여 용접 상태를 평가합니다.
작동 원리
- 광학 센서(포토다이오드, 분광기 등)가 특정 파장 또는 전체 스펙트럼을 계측.
- 플라즈마의 광강도와 키홀(keyhole) 안정성을 분석하여 용접 상태를 판단.
- 주로 자외선(UV), 가시광선(VIS), 적외선(IR) 센서를 사용.
특징 및 적용 사례
- 플라즈마 신호 분석: 용접 상태와 플라즈마의 거동을 밀접하게 분석 가능.
- 키홀 및 용융풀 상태 평가: 키홀의 압력 변화와 용융풀의 온도 분포를 시각적으로 파악.
장점
- 정밀 데이터: 플라즈마의 광강도 및 키홀 거동 정보를 정밀하게 수집.
- 비접촉 방식: 용접 공정에 영향을 미치지 않음.
단점
- 내부 결함 탐지의 어려움: 표면 결함 중심으로 데이터 수집.
- 고가의 장비: 고성능 센서 및 필터 설계가 요구됨.
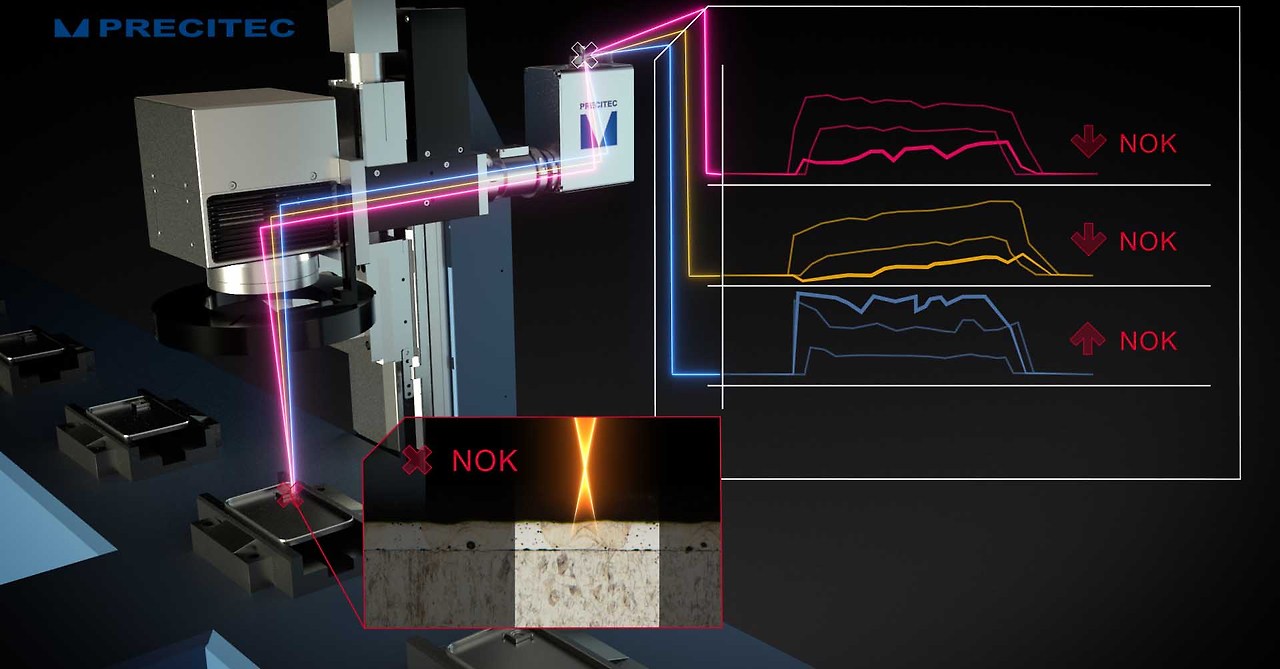
(3) 카메라를 이용한 모니터링
CCD 또는 CMOS 카메라를 사용하여 용융풀과 키홀의 움직임을 관찰하며 용접 상태를 모니터링합니다.
작동 원리
- 레이저 빔과 동축(co-axial)으로 카메라를 설치하거나, 외부에 카메라를 배치하여 용접 상태를 영상으로 기록.
- 고속 카메라를 사용해 키홀 및 용융풀의 거동을 실시간으로 분석.
특징 및 적용 사례
- 시각적 데이터 제공: 용접 상태를 직관적으로 확인 가능.
- 용융풀 상태 관찰: 용접 속도 및 열원 이동에 따른 용융풀 형상 변화 감지.
장점
- 직관적 관찰: 용접 상태와 형상을 시각적으로 확인 가능.
- 유연성 높은 설치: 카메라 위치와 각도를 조정하여 다양한 환경에 적용 가능.
단점
- 데이터 처리 시간: 고속 카메라로 얻은 데이터를 분석하는 데 시간 소요.
- 장비 고비용: 고성능 IR/UV 카메라 비용이 높음.

(4) 분광 분석을 이용한 모니터링
레이저 용접 시 발생하는 플라즈마에서 방출되는 특정 스펙트럼 정보를 분석하여 품질을 평가합니다.
작동 원리
- 분광기(Spectrometer)를 통해 플라즈마 스펙트럼 신호를 계측.
- 특정 금속 원자의 스펙트럼 강도를 분석하여 용접 품질을 예측.
특징 및 적용 사례
- 스펙트럼 데이터 활용: 금속 원자의 분석 및 용접 상태 평가.
- 플라즈마 안정성 평가: 용접 중 플라즈마 강도의 시간 변화를 통해 품질 판단.
장점
- 정밀 분석 가능: 플라즈마 상태와 품질 간의 높은 상관성 제공.
- 연구 활용성: 고급 분석 도구로 연구 및 개발에 적합.
단점
- 비용 문제: 고가의 장비와 샘플링 시스템 필요.
- 샘플링 속도 한계: 실시간 분석에는 제약이 있을 수 있음.
4️⃣ 레이저 용접 모니터링 기술의 장단점 비교
기술 종류 | 장점 | 단점 |
음향 신호 | 비파괴 방식, 실시간 모니터링 가능 | 소음에 민감, 접촉식 센서의 적용 한계 |
광 신호 | 정밀한 플라즈마 데이터 제공, 비접촉 방식 | 내부 결함 탐지 어려움, 고가 장비 필요 |
카메라 | 시각적 데이터 제공, 다양한 환경에 적용 가능 | 데이터 처리 시간 소요, 고비용 |
분광 분석 | 금속 원소 분석, 품질 정밀 예측 가능 | 고비용, 실시간 샘플링 속도 제약 |
5️⃣ 결론: 레이저 용접 모니터링 기술의 중요성
이들 기술은 각각의 강점과 한계를 가지고 있지만, 용접 품질 보증의 다양한 요구 사항을 충족시키기 위해 서로 보완적으로 활용될 수 있습니다. 특히, 고품질 배터리 생산에서 결함을 사전에 방지하고 재작업과 생산 중단을 최소화하기 위해 이러한 모니터링 기술은 점점 더 중요해지고 있습니다.
향후에는 AI(인공지능)와 빅데이터 분석 기술과 결합하여 더욱 정교하고 예측적인 품질 관리가 가능할 것입니다. 실시간 데이터 수집과 분석 기술이 발전함에 따라, 용접 공정에서 발생하는 미세한 변화를 감지하고 이를 기반으로 결함 발생 가능성을 사전에 예측할 수 있을 것으로 기대됩니다.
레이저 용접 모니터링 기술은 단순히 품질 관리의 도구를 넘어, 배터리 제조 산업의 경쟁력을 높이는 핵심 기술로 자리 잡고 있습니다. 지속적인 연구와 기술 발전을 통해 모니터링 시스템은 더욱 혁신적으로 진화할 것이며, 배터리 산업의 성장을 견인하는 중요한 요소가 될 것입니다.
'▶ Battery > -. technology' 카테고리의 다른 글
⚡ 배터리 제조 공정 속 금속 재결정 이해하기 | 집전체 재결정 및 기계적 성질 상관관계 📊 (0) | 2024.12.14 |
---|---|
💡 배터리 음극 집전체의 핵심 소재! 전해 동박 인장 강도와 연신률 중요성 및 제어법 완벽 정리 (0) | 2024.12.10 |
🌐 나트륨 이온 배터리의 주요 특징, 장점과 단점 그리고 글로벌 기술 현황과 시장 선도 기업은? (0) | 2024.11.28 |
🔋 블레이드 셀이란? 혁신적인 자동차 배터리 기술의 특징과 장점 🌟 (0) | 2024.11.25 |
🚀 배터리 집전체 혁신! 고분자 복합 구리 포일(Polymer Composite Copper Foil)의 소개, 개발 배경과 기술적 특징 (0) | 2024.11.22 |