배터리 제조 과정에서 조립 공정은 전극과 분리막을 조합하여 배터리 셀을 완성하는 단계로, 배터리의 성능과 안전성에 큰 영향을 미칩니다. 이 과정에서 사용되는 주요 기술 중 하나가 **와인딩(Winding)**과 스택(Stacking) 공정입니다. 이번 글에서는 두 공정의 정의, 작동 원리, 장단점, 그리고 스택 공정의 다양한 방식에 대해 자세히 살펴보겠습니다.
1. 조립 공정이란?
조립 공정은 배터리 제조에서 전극, 분리막, 전해질 등의 구성 요소를 조합하여 완전한 배터리 셀을 만드는 단계입니다. 이 과정은 전극과 분리막을 올바르게 배치하고, 셀 내에서 화학적 및 물리적 안정성을 보장하기 위해 필수적입니다. 조립 공정은 배터리의 최종 성능, 수명, 안전성에 큰 영향을 미치며, 각 요소가 정밀하게 결합되어야 효율적인 에너지 저장 및 방출이 가능합니다.
2. 조립 공정 중요성
- 성능 최적화: 정확한 조립은 배터리의 전기적 특성을 최적화하여 에너지 밀도, 출력, 효율성을 향상시킵니다. 잘못된 조립은 전기 저항 증가, 비효율적인 전류 흐름 등을 초래할 수 있습니다.
- 안전성 향상: 조립 과정에서의 결함은 단락이나 열폭주와 같은 위험을 증가시킬 수 있습니다. 특히, 전극과 분리막의 정확한 위치와 균일한 조립은 셀 내의 안전성을 보장합니다.
- 제품 수명 연장: 균일한 조립은 셀의 내부 스트레스를 줄이고, 충방전 사이클 동안 물리적 변형을 최소화하여 배터리의 장기적인 안정성과 수명을 연장합니다.
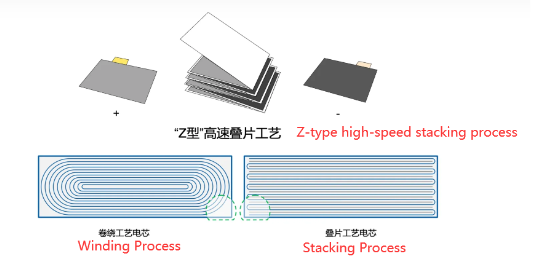
3. 와인딩(Winding) 공정 🌀
와인딩 공정은 양극판, 음극판, 분리막을 롤 형태로 감아 '젤리롤(Jelly Roll)' 구조를 만드는 방식입니다. 이 방식은 주로 원통형 셀과 각형 셀에서 사용됩니다.
- 작동 원리:
- 양극판과 음극판 사이에 분리막을 삽입합니다.
- 이 조합을 롤러를 이용해 감아 올립니다.
- 감긴 형태가 '젤리롤'처럼 보이며, 이를 금속 캔에 삽입해 밀봉합니다.
- 장점 🌟:
- 생산 효율성: 와인딩 공정은 연속적인 작업이 가능하여 대량 생산에 적합합니다.
- 비용 절감: 기계 설비와 공정이 단순하여 제조 비용이 상대적으로 낮습니다.
- 단점 ⚠️:
- 공간 활용의 비효율성: 감긴 구조로 인해 내부 공간을 완벽하게 채우지 못해 에너지 밀도가 낮아질 수 있습니다.
- 열 관리의 한계: 내부 공간이 밀폐되어 있어 열 방출이 어려워질 수 있습니다.
- 적합성:
- 원통형 셀에 적합하며, 특정 각형 셀에서도 사용할 수 있습니다. 원통형 셀에서는 공간 효율성보다는 대량 생산성과 구조적 안정성이 중요하므로 와인딩 방식이 적합합니다.
4. 스택(Stacking) 공정 🏗️
스택 공정은 양극판, 음극판, 분리막을 층층이 쌓아 올려 스택(Stack)을 만드는 방식으로, 주로 파우치형 셀과 각형 셀에서 사용됩니다.
- 작동 원리:
- 전극과 분리막을 순차적으로 층층이 쌓아 올립니다.
- 이 층을 외부 포장재로 감싸 밀봉하여 배터리 셀을 완성합니다.
- 장점 🌟:
- 높은 에너지 밀도: 공간을 효율적으로 사용하여 셀의 에너지 밀도가 높아집니다.
- 구조적 안정성: 층층이 쌓인 구조는 내구성이 높고 열 관리가 용이합니다.
- 단점 ⚠️:
- 생산 속도: 각 층을 개별적으로 쌓아야 하므로 와인딩 방식에 비해 생산 속도가 느립니다.
- 제조 비용: 정밀한 장비와 기술이 필요하여 초기 투자 비용이 증가할 수 있습니다.
- 적합성:
- 각진 형태가 필요한 파우치형 셀 및 각형 셀에 적합합니다. 이러한 셀들은 공간 활용이 중요하며, 스택 공정은 이러한 형태에서 내부 공간을 최적화할 수 있습니다.
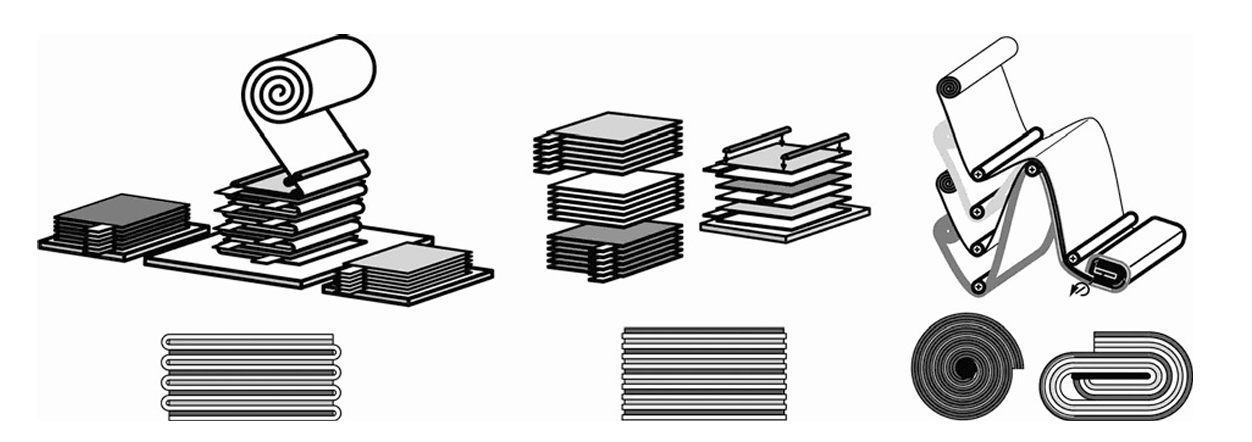
5. 스택 공정의 종류 🔍
- 스택(Stacking) 공정은 전극과 분리막을 층층이 쌓아 올리는 방식으로, 배터리의 구조적 안정성과 에너지 밀도를 높이는 데 중요한 역할을 합니다. 스택 공정은 쌓는 방식에 따라 여러 가지로 분류되며, 각 방식은 배터리의 용도와 성능 요구에 따라 선택됩니다. 주요 스택 공정 종류는 다음과 같습니다:
(1) 직접 스태킹(Direct Stacking)
- 설명: 전극과 분리막을 하나씩 순서대로 쌓아 올리는 전통적인 방식으로, 각 층이 개별적으로 분리되어 있습니다.
- 장점: 구조가 단순하여 설계가 용이하며, 다양한 셀 형태에 적용 가능합니다. 특히, 수작업으로도 쉽게 수행될 수 있어 소규모 생산이나 연구개발 단계에서 유용합니다.
- 단점: 개별 층을 하나씩 쌓아야 하기 때문에 공정 속도가 느리고, 대량 생산에 비효율적입니다. 또한, 각 층 간의 일관성을 유지하는 것이 어려워 품질 변동이 발생할 수 있습니다.
- 설명: 분리막을 지그재그 형태로 접으면서 그 사이에 전극을 삽입하는 방식으로, 연속적인 작업이 가능합니다.
- 장점: 공정 속도가 빠르고, 자동화가 용이하여 대량 생산에 적합합니다. 분리막이 연속적으로 이어져 있어 전극의 위치를 일관되게 유지할 수 있습니다.
- 단점: 분리막의 연속성이 요구되므로 고도의 품질 관리가 필요하며, 공정 중에 분리막이 손상되면 전체 구조에 영향을 미칠 수 있습니다.
- 설명: 전극과 분리막을 미리 결합하여 하나의 층으로 만든 후, 이를 여러 층으로 쌓는 방식입니다.
- 장점: 공정이 효율적이고, 층간 결합이 강하여 구조적 안정성이 높습니다. 특히, 자동화된 공정에서 높은 생산성을 유지할 수 있으며, 품질 관리가 용이합니다.
- 단점: 초기 설비 투자 비용이 높으며, 복잡한 장비가 필요합니다. 또한, 공정의 복잡성으로 인해 설정과 유지보수가 까다로울 수 있습니다.
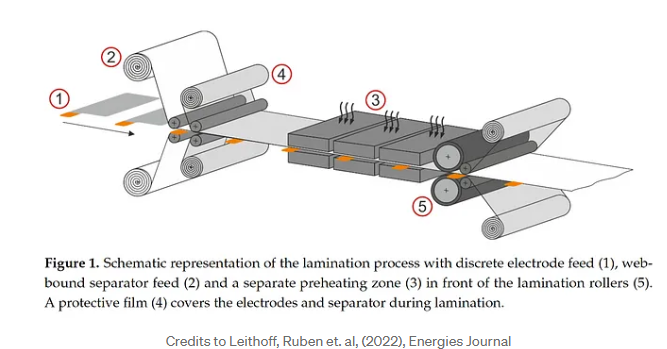
6. 결론 🚀
와인딩과 스택 공정은 각각의 장단점과 특성을 가지고 있으며, 배터리의 용도와 요구 사항에 따라 적합한 공정을 선택하는 것이 중요합니다. 와인딩 공정은 원통형 셀에서 대량 생산성과 구조적 안정성에 적합하며, 스택 공정은 각형 및 파우치형 셀에서 높은 에너지 밀도와 공간 활용이 중요한 경우에 유리합니다. 이러한 공정 선택은 배터리 제조사와 제품의 최종 성능에 큰 영향을 미치므로, 신중한 접근이 필요합니다.
'▶ Battery > -. technology' 카테고리의 다른 글
🔋 배터리 혁신! Cell to Pack(CTP) 기술의 시작과 CATL CTP 세대별 발전 특징 분석 🧐 (0) | 2024.11.10 |
---|---|
특허 분석] CATL, 단결정입자 활용, 전극설계 최적화, 공극률제어 (1) | 2024.11.08 |
🔍 배터리 제조의 시작, 슬러리 믹싱 공정 – 중요성, 믹싱/혼합 방법, 품질 기준, 제어 요소 총정리! (0) | 2024.11.02 |
🔍 배터리 제조의 필수 공정: 코팅 공정과 Wet Coating 핵심과 주요 변수 (2) | 2024.11.01 |
⚡ 리튬이온 배터리 고속충전의 핵심 원리와 주요 파라미터 🔋 (0) | 2024.10.31 |